Rigid, heavy-duty machining center demonstrated with modular automation system
FLORENCE, Ky., Oct. 8, 2013 – At DISCOVER 2013, Mazak demonstrated the power and versatility of its HORIZONTAL CENTER NEXUS (HCN) 6800-II horizontal machining center while integrated into the company’s modular pre-engineered PALLETECH Manufacturing System. The highly productive unattended manufacturing cell included a tilt/rotate load station, six-pallet stocker and rail-guided pallet loader.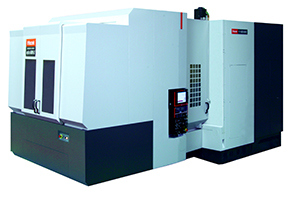
As the base machine in the cell, the HORIZONTAL CENTER NEXUS 6800-II featured a 10,000-rpm, 50-hp spindle. It is the standard of the three integral motor spindle types – standard, high-speed and high-torque – Mazak offers for the machine. With these three choices, shops can match spindle speed and power to their specific machining requirements for any materials from steels to nonferrous metals, thus ensuring fast and efficient part processing.
A two-pallet changer is standard with the HORIZONTAL CENTER NEXUS 6800-II and pre-engineered to interface with Mazak’s PALLETECH system for lights-out operation. The machine’s pallet size is 24.80” x 24.80” (630 mm x 630 mm), with a maximum load capacity of 3,307 lbs (1,500 kg).
Mazak’s PALLETECH system offers three pallet stocker configurations – flat/single level, two level and three level. PALLETECH provides flexibility in production and is efficient both in high-mix, low-volume production or high-volume production. And as a shop’s business grows, PALLETECH can grow with it thanks to its modular, pre-engineered construction. As such, PALLETECH accommodates up to 16 machines, six to 240 pallets and as many as eight loading stations.
Using Mazak’s PMC-WEB cell controller software over standard PCs and networks, shop management can monitor operations, view and change schedules on-the-fly, manage part program files from anywhere on the network, track tool life/breakage and issue instructions to the shop floor. Users are able to interrupt a planned machining queue and produce an emergency part to meet demands. Furthermore, users can perform scheduling by pallet or workpiece number and initiate cell production with a simple push of a button.
For large-part capability within the cell, the HORIZONTAL CENTER NEXUS 6800-II provides axis travels measuring 41.34" (1,050 mm) in X, 35.43” (900 mm) in Y and 38.58" (980 mm) in Z, and the machine incorporates Mazak’s MX Hybrid Roller Guide System to deliver levels of durability and reliability that result in long-term accuracy. The innovative way system increases vibration dampening, extends tool life, handles higher load capacities and eliminates tramp oil in the coolant by utilizing a greener grease-based lubrication system.
The HORIZONTAL CENTER NEXUS 6800-II’s NC rotary table rotates 90 degrees in 1.9 seconds and features 0.001-degree minimum increments for precise four-axis indexing and machining. The table incorporates Mazak’s high-precision 360-degree position coupling and accommodates workpiece sizes up to 41.34” (1,050 mm) in diameter and 51.18” (1,300 mm) high.
Cam-driven tool changing on the HORIZONTAL CENTER NEXUS 6800-II contributes to reductions in non-cut times by ensuring fast and reliable 5.2-second chip-to-chip tool change cycles. The machine’s automatic tool changer stores up to 43 tools and accommodates maximum tool diameters of 10.24” (260 mm).
Additionally, Mazak offers an expandable tool hive, which easily incorporates into a PALLETECH machining cell to provide flexible machining capability. The hive’s basic frame starts with a 180-tool capacity and is expandable to 204 tools or 240 tools after installation. Another basic hive frame offers 240 tools initially and is later expandable to 288, 312 or 348 tool capacities.