Vertical turning center delivers multi-tasking functionality for large part processing
FLORENCE, Ky., Oct. 8, 2013 – At DISCOVER 2013, Mazak showcased the pure power and size capability of its new MEGATURN NEXUS (MTN) 1600M CNC vertical turning center. The machine excels in the heavy-duty cutting of large, low-to-medium profile, tough-to-machine workpieces such as those found in the construction machinery and jet engine industries.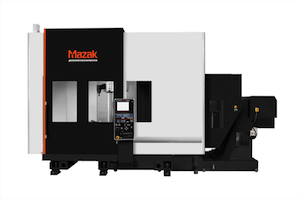
Mazak constructed the machine specifically for removing large amounts of metal from challenging materials, including stainless steel, titanium, and other alloys. With rotary tool milling capability, the machine combines turning and secondary machining operations to improve part accuracy and increase productivity through Multi-Tasking operations and the reduction of set ups and workpiece handling.
At the heart of the MEGATURN NEXUS 1600M is a powerful, rigid, high-torque integrated main drive motor/spindle with a maximum speed of 350 rpm and maximum torque of 7,405 ft-lbs. It can accommodate workpieces measuring up to 64.96” in diameter, 35.43” high and weighing as much as 11,023 lbs. For increased spindle up time, the machine can be outfitted with an optional two-pallet changer.
The machine’s 12-tool drum-style turret provides fast indexing and features a live rotary tool spindle with a maximum speed of 3,000 rpm and 103 ft-lbs. of torque for milling and drilling operations to eliminate the need for transferring big heavy workpieces to other machines for secondary operations. For efficient large boring bar work, the turret accommodates shank diameters up to 2”. Mazak also offers an optional automatic tool changing system for the MEGATURN NEXUS 1600M.
Equipped with Mazak’s MATRIX NEXUS 2 CNC control, the machine increases versatility by allowing for both conversational and EIA-ISO programming. It provides simultaneous control of three axes and continuous control of second spindles to deliver fast and precise multi-tasking part processing.